The amprove team consists of the founders Dennis Middelmann, Yannik Eggert and Rami Bedewi. The three met while they were employed in the automotive industry, during which the idea to found amprove first began.
Dennis graduated with a bachelor's degree in mechanical engineering from the Technical University of Central Hesse in 2018 and afterwards completed his master's degree in mechanical engineering at the University of Stuttgart. During his studies, he spent two years in R&D at an automotive company, where he worked on component development, specifically simulation-based structural optimization.
Yannik completed his automotive engineering bachelor's degree at Ulm University of Technology with a focus on design and development in July 2019, and has been working full-time on the startup since then. As a motorsport enthusiast, he developed a keen interest in performance and lightweight design, which is why he worked on structural optimization for additive manufacturing in the automotive industry.
Rami completed his bachelor’s degree in mechanical engineering with a minor in entrepreneurship and management at Johns Hopkins University in 2016. He then moved to Germany, where he completed several internships in the automotive industry focusing also on the area of R&D for component development in both series production and motorsports vehicle applications. At the same time, he also completed his master's degree in the Computational Mechanics of Materials and Structures (COMMAS) program at the University of Stuttgart.
amprove is a development service provider and supplier of high-performance structural components. To develop these components, the conventional design process is replaced by a simulation-based process chain. This makes it possible to generate more complex geometries that are tailored to fit the specific application, which achieve an efficient material distribution that both minimizes the material usage while also maximizing various performance metrics. In addition, the development time of the components is drastically reduced by eliminating the manual design iterations that are required in the conventional process.
At its core, the development processed is based around modularity, so that the various input parameters can be changed to suit the desired application and still achieve the ideal result. Therefore, amprove can use the process to develop components for high-volume production through, or, in cases where the performance of the component is a priority, or small quantities are given, the component can be optimized for 3D printing. By implementing such a process to generate lightweight structures, the customer benefits through lower material consumption, improved component properties and a myriad of secondary effects depending on the use case, such as increased travel speed of production equipment or reduced energy requirements to power this equipment.
The goal of component optimization is not limited to structural properties. It could also be to improve thermal properties so that temperature problems are eliminated by an optimized material distribution. Depending on the application, the customer benefits, for example, through less wearing throughout the life of the part, higher performance of thermally stressed components and the saving of additional sources of cold and heat generation. To identify components with a high optimization potential, amprove offers an opportunity for rapid feedback by uploading CAD data to their website.
Contact
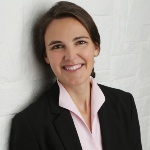
Melanie Minderjahn
Career Service - Inner Development, Public Relations